The Process of Plastics Rotomolding: How It Works and Why It Matters
The Process of Plastics Rotomolding: How It Works and Why It Matters
Blog Article
Rotational molding, or rotomolding, is now an essential production process in today's industry, particularly in regards to plastics. This adaptable technique has permitted companies across numerous industries to innovate and generate sturdy, cost-effective, and customizable products. But wherever, just, is this approach being employed the most? Here's a closer go through the major applications of Parts Rotomolding and the huge benefits it brings.
What Makes Rotomolding Popular for Plastic Services and products?
Before we break down its varied programs, it's worth noting why is rotomolding stay out. Unlike different production methods, the method consistently distributes materials over the mold for consistent wall thickness and remarkable durability. Their flexibility suggests it suits special styles and numerous industries easily — the versatility is unmatched.

Important Programs of Plastics Rotomolding
1. Storage and Water Tanks
One of many greatest uses of materials rotomolding is in the creation of storage and water tanks. Whether for agricultural, commercial, or residential applications, rotomolded tanks are prized because of their durability, weight to weather problems, and leak-proof construction. These tanks frequently function complex types that take advantage of the accuracy of rotational molding.
2. Automotive Components
From gasoline tanks to air tubes and defensive covers, rotomolding represents a substantial role in the automotive industry. Automotive parts require light, sturdy, and durable materials to improve vehicle performance, and that manufacturing strategy provides only that. The ability to develop one-piece, smooth elements assures long-lasting performance.
3. Outside Furniture and Playground Gear
Creating outside furniture and playground components is yet another important application. Rotomolding assures these items are UV-resistant, resilient against the elements, and safe for many users. Like, colorful playground models and counter seating benefit from customization options accessible via that process.
4. Professional Equipment
Rotomolded plastics are also generally used in industrial controls for components like hoppers, bins, and equipment housing. These parts need to withstand major use, harsh conditions, and potential wear. The toughness and power to produce powerful components have situated rotomolding as an ideal approach for such needs.
5. Consumer Services and products
Sets from kayaks and refrigerators to bins and planters stalks from rotomolding. These consumer services and products demand a high-quality, cost-efficient production strategy to ensure toughness without compromising design. Rotomolding ticks every box.
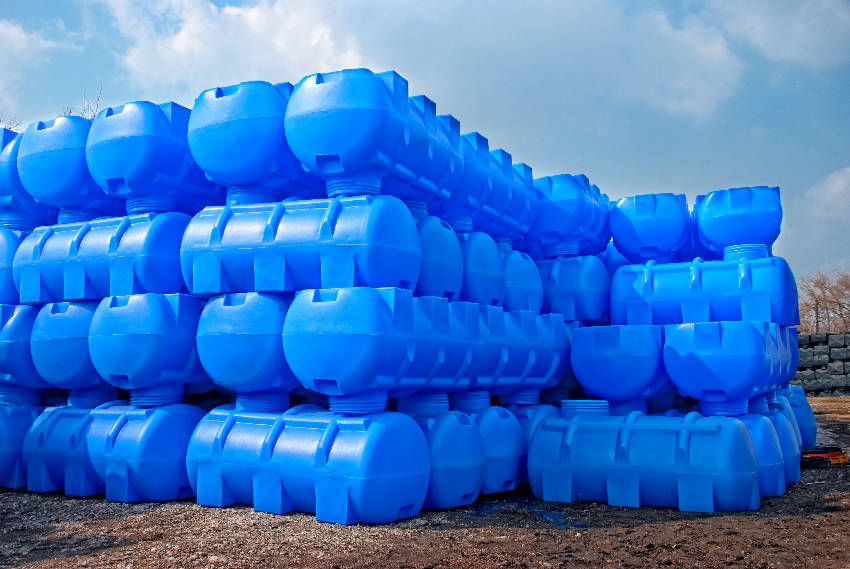
The Benefits of Rotomolding
The value of parts rotomolding does not stop at their diverse applications. Industries carry on to select this process because it:
Enables Modification: Build elaborate shapes, dimensions, and textures unmatched by other production processes.
Increases Longevity: Creates easy, crack-resistant services and products well suited for varied conditions.
Reduces Charges: Reduced tooling expenses allow it to be a good selection for both small and large runs.
Supports Sustainability: Rotomolded products are often recyclable, aligning with the growing force toward eco-friendly practices.
Surrounding the Potential with Pockets Rotomolding
From everyday client what to important professional instruments, materials rotomolding stands apart as an essential production technique in today's market. Its versatility, cost-effectiveness, and toughness guarantee its extended development as an industry favorite. Report this page